The Ultimate Guide To Alcast Company
Table of ContentsNot known Details About Alcast Company The Only Guide for Alcast CompanyThe Greatest Guide To Alcast CompanyGetting The Alcast Company To WorkThe Alcast Company IdeasTop Guidelines Of Alcast CompanyAlcast Company Things To Know Before You BuyThe Buzz on Alcast Company
It possessed good stamina and machinability. There are numerous other aluminum alloys that can be utilized for casting components. To locate out which alloys would certainly be great for your jobs, call Impro.
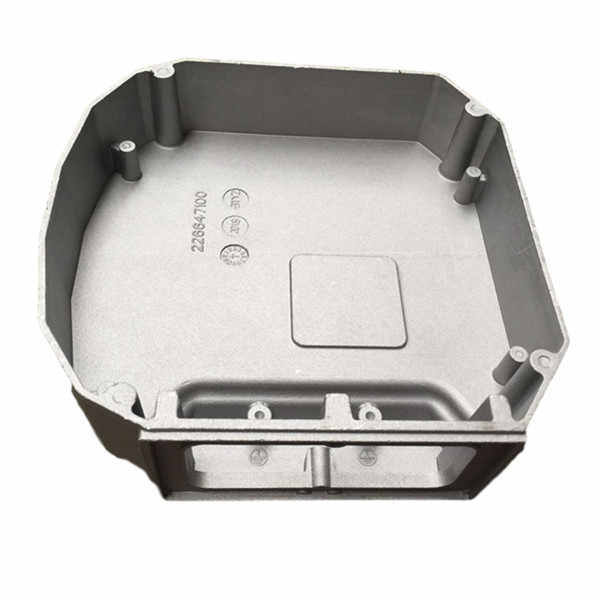
Various components and quantities generate a wide range of desirable physical and chemical residential or commercial properties. And the Aluminum Organization (AA), based in The United States and copyright, has developed specifications that manage light weight aluminum alloys' composition, buildings, and classification. There are two sorts of aluminum alloys functioned and cast. Factory employees form these alloy kinds in various means, which substantially impacts their attributes.
Alcast Company Can Be Fun For Anyone
Cast light weight aluminum alloys are made by melting pure aluminum and incorporating it with various other steels while in fluid type. Then the mix is poured into a sand, die, or financial investment mold. After solidification, the steel is eliminated from its mold. At this phase, it is in either its final kind or as a billet or ingot for additional processing.
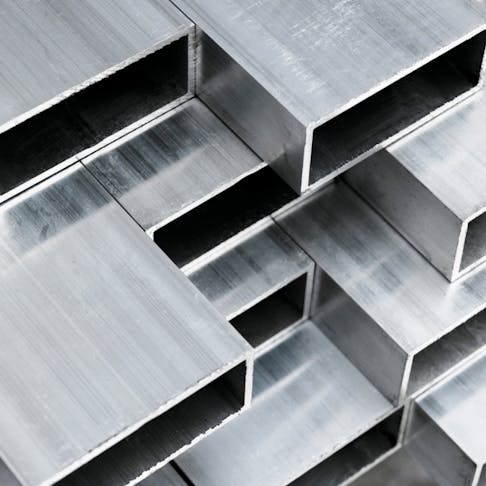
There are many minor differences in between wrought and cast light weight aluminum alloys, such as that cast alloys can include extra substantial amounts of other metals than wrought alloys. But the most significant distinction in between these alloys is the construction procedure whereby they will certainly most likely to deliver the end product (aluminum metal casting). Apart from some surface area treatments, cast alloys will exit their mold in virtually the exact strong kind preferred, whereas functioned alloys will undertake several modifications while in their solid state
A Biased View of Alcast Company
If you think that a wrought alloy may be the best for your job, take an appearance at a few of our short articles that discuss even more about certain wrought alloys, such as Alloy 6061 and Alloy 6063. On the various other hand, if you believe an actors alloy would be better for you, you can find out more about some actors alloys in our Alloy 380 and Alloy 383 articles (coming soon).
When selecting a light weight aluminum foundry for your production requirements, it's essential to examine a number of factors. One of one of the most critical aspects to take into consideration is the experience and skills of the shop. Selecting a factory who has the best understanding of the light weight aluminum casting process, and the profile to reveal for it, helps to have an effective end result for your task.
Not known Details About Alcast Company
Having the experience and sector understanding to engineer your castings for optimal production and top quality end results will certainly enhance the job. Producing aluminum castings needs a complicated set of processes to attain the ideal results. When selecting a new light weight aluminum factory to partner with, guarantee they have considerable market experience and are educated concerning all elements of the light weight aluminum casting process: style, production, material analysis, and product screening.
The foundry should also have a tried and tested record of supplying extraordinary items that fulfill or surpass customer assumptions. Quality assurance needs to additionally be at the top of your list when selecting an aluminum foundry. By working with a qualified factory that adheres click now to the standards for quality assurance, you can protect the stability of your product and guarantee it meets your specs.
8 Simple Techniques For Alcast Company
By picking a firm that provides services that satisfy or surpass your product needs, you can be certain that your project will certainly be finished with the utmost accuracy and effectiveness. Various components call for different manufacturing methods to cast light weight aluminum, such as sand spreading or die casting.
Die casting is the name offered to the process of producing complicated metal elements through usage of mold and mildews of the part, additionally understood as dies. It generates even more elements than any kind of various other process, with a high level of accuracy and repeatability. There are 3 sub-processes that fall under the group of die spreading: gravity pass away spreading (or long-term mold and mildew spreading), low-pressure die casting and high-pressure die spreading.
What Does Alcast Company Do?
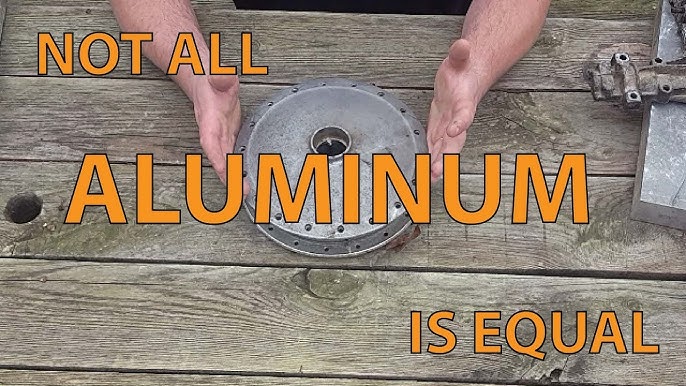
The pure steel, likewise understood as ingot, is included to the heating system and maintained the molten temperature level of the steel, which is then moved to the injection chamber and injected right into the die. The pressure is after that preserved as the metal strengthens. Once the steel strengthens, the cooling process starts.
The thicker the wall of the component, the longer the cooling time since of the quantity of interior metal that also requires to cool. After the element is totally cooled down, the die cuts in half open and an ejection mechanism pushes the component out. Following the ejection, the die is closed for the next injection cycle.
Fascination About Alcast Company
The flash is the additional material that is cast throughout the process. Deburring gets rid of the smaller pieces, called burrs, after the trimming procedure.
Today, top makers utilize x-ray screening to see the entire interior of components without cutting right into them. To obtain to the ended up item, there are 3 primary alloys made use of as die spreading material to pick from: zinc, aluminum and magnesium.
Zinc is among the most pre-owned alloys for die spreading because of its reduced price of raw products. It's likewise among the stronger and steady metals. And also, it has exceptional electrical and thermal conductivity. Its rust resistance also permits the components to be long-term, and it is among the much more castable alloys as a result of its lower melting factor.
The Buzz on Alcast Company
As pointed out, this alloy is among one of the most generally utilized, yet manufactures will, sometimes, pick light weight aluminum over zinc because of light weight aluminum's manufacturing advantages. Aluminum is very affordable and one of the a lot more flexible alloys. Aluminum is made use of for a variety of different products and industries anything from home window frames to aerospace products.